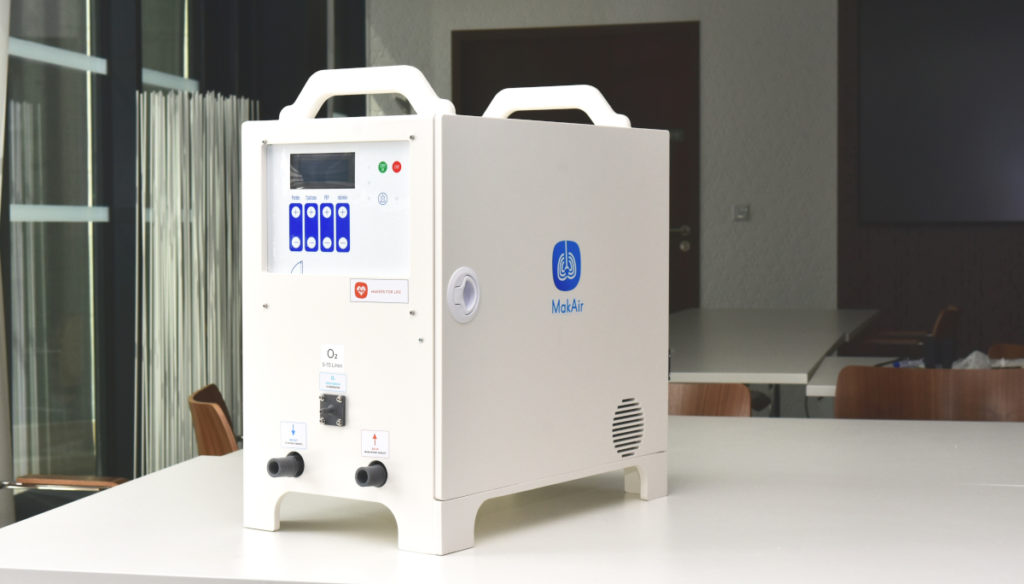
Face à l’urgence sanitaire liée à la pandémie de COVID-19, le collectif français « Makers For Life” né de l’initiative d’entrepreneurs nantais, de makers, de chercheurs, de professionnels de santé et d’ingénieurs a mis au point le MakAir, un respirateur artificiel dédié au traitement du COVID-19. Grâce aux synergies déployées depuis le 17 mars dernier, par le collectif avec l’Université de Nantes, le CHU de Nantes, le CEA mais aussi le soutien de nombreux industriels, collectivités et l’Agence d’Innovation de la Défense, le MakAir attend désormais l’autorisation de l’ANSM (Agence Nationale de Sécurité du Médicament) pour démarrer les essais cliniques et la production en volume.
Il pourrait être utilisé pour traiter les insuffisances respiratoires liés au COVID-19 au sein des établissements hospitaliers Français en soutien des dispositifs existants et dans les pays faisant face à des pénuries de respirateurs. La marque d’électroménager SEB va produire les 500 premiers exemplaires de ce respirateur à bas coût.
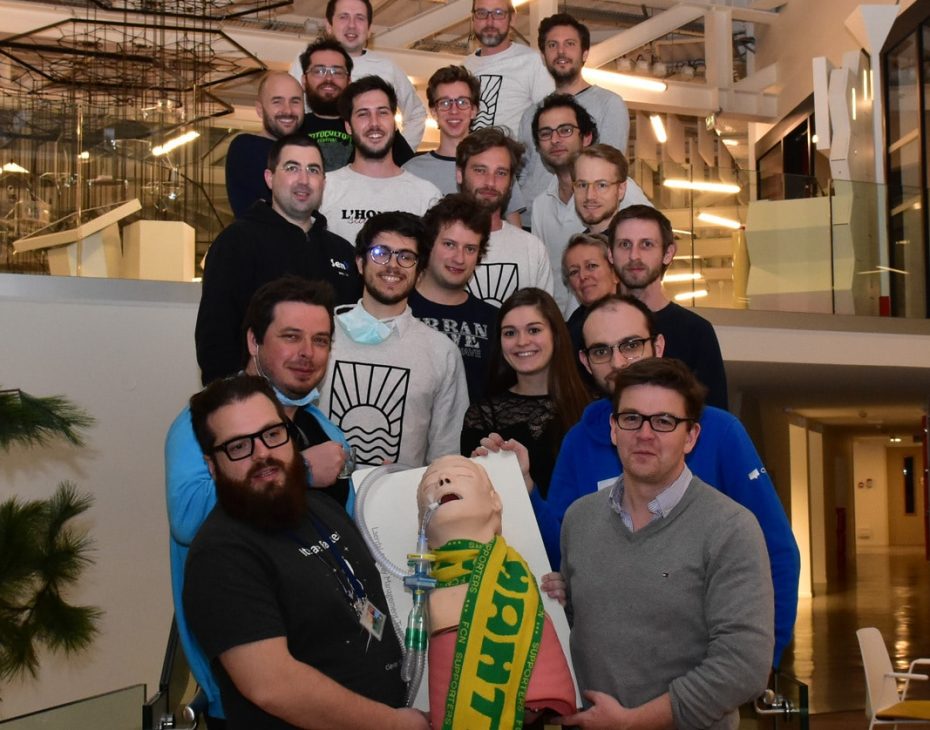
Travaillant dans le domaine de l’impression 3D avec mon entreprise de prototypage rapide QB Maker, j’ai été contacté par Quentin Adam l’un des fondateurs du projet pour mettre à disposition mes compétences et mes imprimantes 3D.
Quand il m’a présenté l’initiative de venir en aide aux hôpitaux en concevant un respirateur artificiel, je lui ai proposé d’aider pour l’impression des prototypes et le dépannage des imprimantes. C’est comme ça que je me suis retrouvé à être le fabmanager du projet.
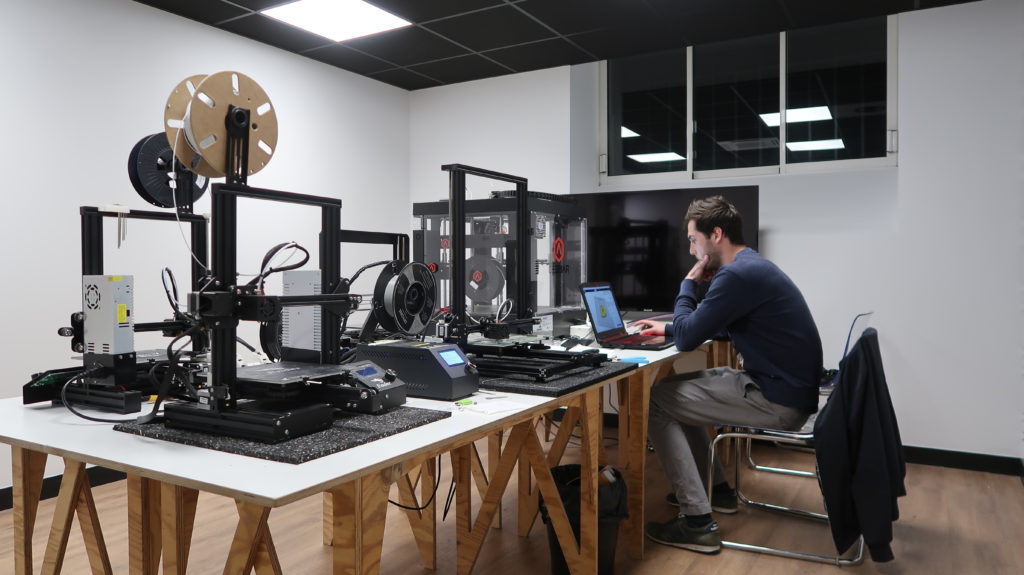
Le MakAir est un respirateur artificiel simplifié exclusivement dédié au traitement de patients atteint du covid-19. C’est un projet 100% open source et non commercial dont le cout de production est évalué à 1 000 € (dix fois moins cher que les respirateurs traditionnels).
Il ne consomme aucun matériel médical : en cette période de crise, l’approvisionnement est un vrai sujet. Des valves aux moteurs en passant par les filtres et les commandes, tout a été conçu et réalisé en partant de matières brutes et composants du marché en utilisant des méthodes de prototypage rapide.
La problématique la plus importante était le temps, il fallait réussir à concevoir rapidement un appareil efficace et qui respecte le cadre réglementaire pour assurer au maximum possible la conformité de notre dispositif.
Enfin la logistique en période de confinement à clairement été notre plus grande difficulté.
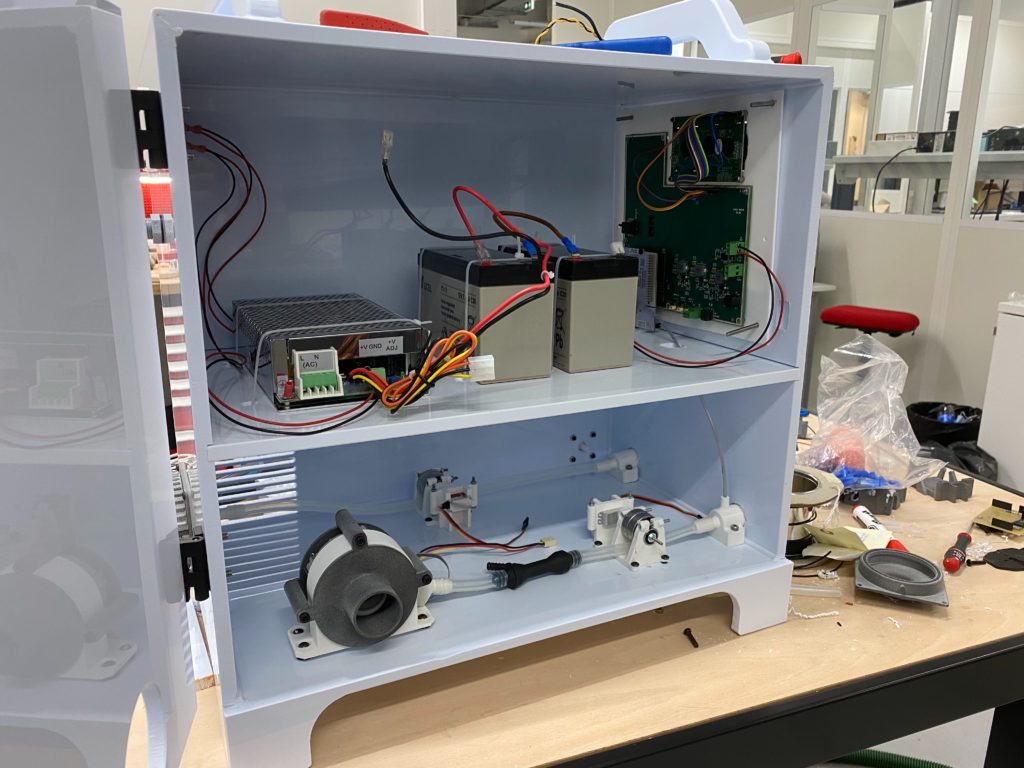
L’enjeu, lorsque l’on développe un produit complexe comme un respirateur artificiel est de respecter les normes et les exigences des dispositifs médicaux.
Dès le départ, le contact avec des dizaines de chercheurs et de professionnels de l’Université de Nantes a permis d’assurer une bonne compréhension des besoins des patients et des médecins réanimateurs.
La première clé c’est la contribution directe des réanimateurs hospitaliers. Nous ne nous sommes pas lancés dans le projet sans avoir impliqué et écouté rigoureusement les professionnels de santé.
La seconde clé, c’est une volonté affirmée, avec des experts du secteur dans l’équipe, de concevoir un dispositif le plus possible en conformité avec les exigences des dispositifs médicaux et organisations de santé (Directives européennes DM et protocole de recherche clinique à valider avec l’ANSM)
Le projet bénéficie de l’expertise scientifique des Professeurs Erwan L’HER (CHU de Brest, CESIM, médecin réanimateur, conseil scientifique) et Pierre Antoine Gourraud (CHU de Nantes, Innovation, anesthésie, réanimation) pour n’en citer que quelques-uns.
Tous ont été intégrés à la démarche de validation des hypothèses et postulats médicaux, et le sont également dans la phase d’évaluation des prototypes.
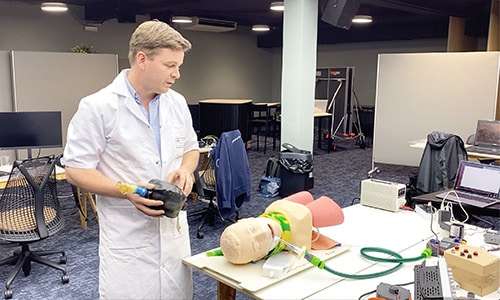
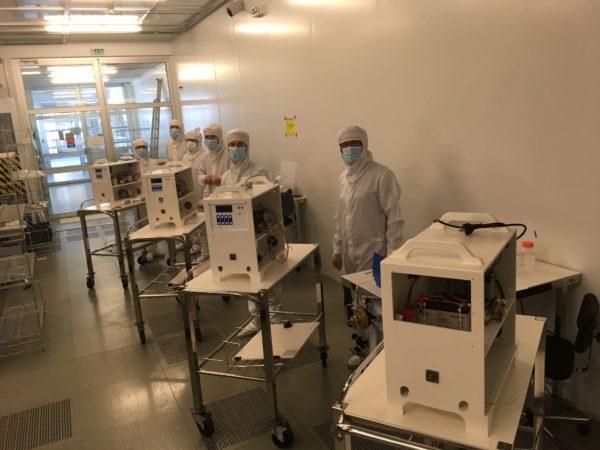
L’impression 3D a joué un rôle important dans le développement du MakAir et sa conception open source permet d’imprimer plusieurs pièces en 3D.
L’un des atouts de l’impression 3D, c’est d’avoir une grande flexibilité de fabrication, pas besoin de moule d’injection plastique, il suffit de modifier le modèle 3D de la pièce et de la relancer en impression.
L’avantage avec ce procédé c’est qu’il nous a été possible de travailler rapidement en lançant plusieurs designs de pièces en parallèle sur les imprimantes 3D et ainsi pouvoir améliorer les pièces en continu.
L’impression 3D raccourcit énormément le délai entre la conception et la fabrication d’un prototype. Il est possible de modifier et d’obtenir en quelques heures une nouvelle pièce !
La majorité des pièces mécaniques du MakAir sont imprimées en 3D, comme :
- Les connecteurs pneumatiques d’entrée et sortie d’air
- La valve de pression
- Le mélangeur d’oxygène (venturi)
- La pièce de maintien du souffleur d’air
- Le filtre de la machine
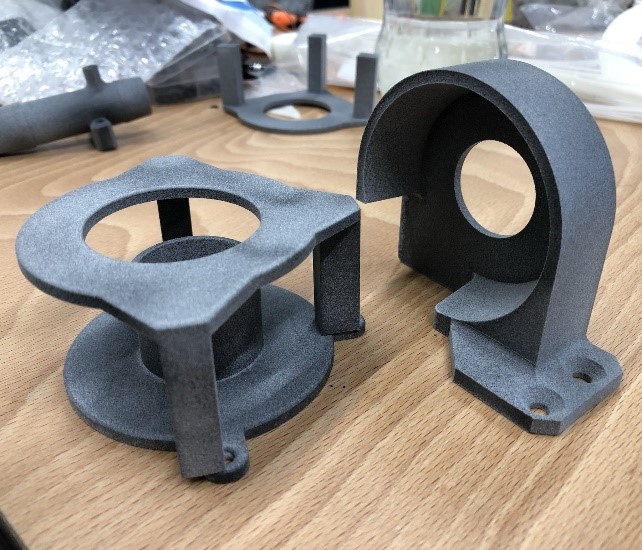
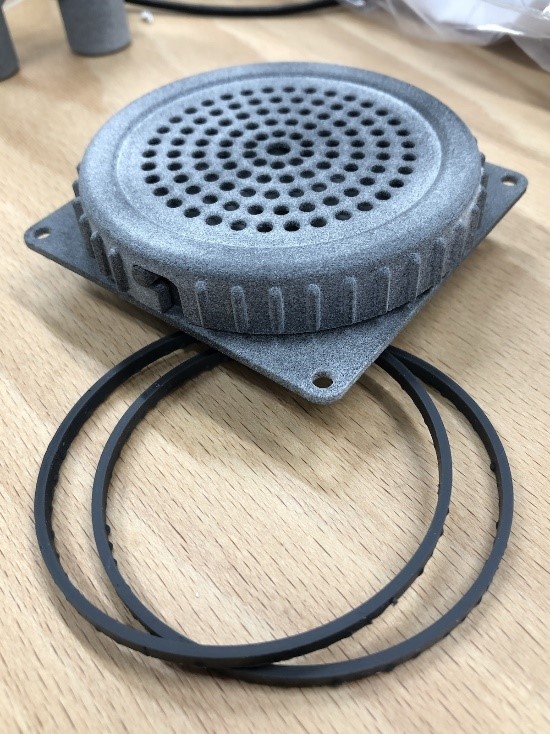
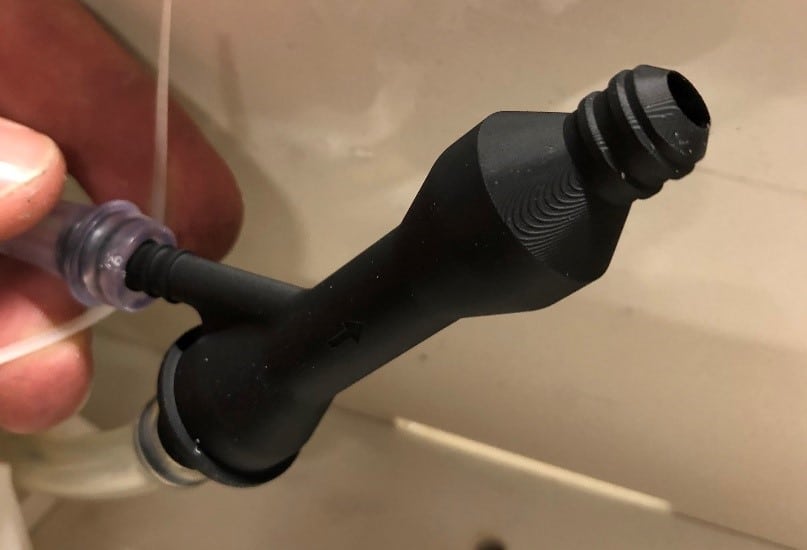
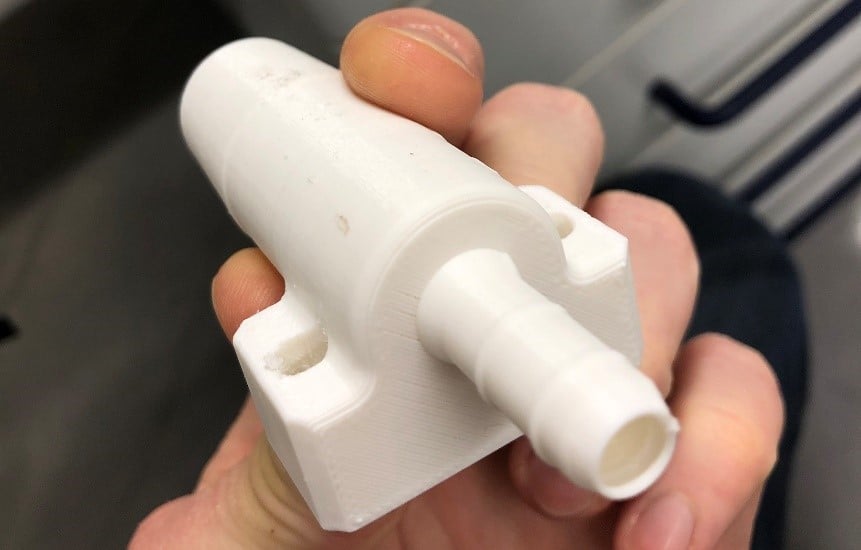
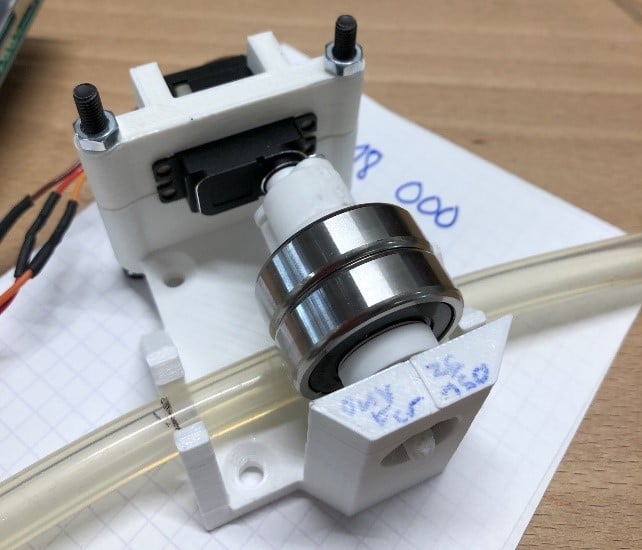
Au démarrage du projet nous ne disposions que de quelques imprimantes, puis un élan de solidarité s’est mis en place pour nous en prêter :
Des particuliers, des professionnels ou encore des écoles, ont mis à disposition leur machines et du matériel très rapidement. On a reçu toutes sortes d’imprimantes : de celles en kit personnalisées aux machines professionnelles. C’est principalement des machines FDM (dépôt de fil fondu) que nous avons utilisé car très répandu et adaptés à nos besoins de prototypes fonctionnels.
Concernant les matériaux, c’était en fonction des stocks que nous avions à disposition mais principalement du PLA car compatible avec toutes les machines et facile à imprimer. Nous avons aussi utilisé du PETG pour certaines pièces nécessitant une plus grande solidité.
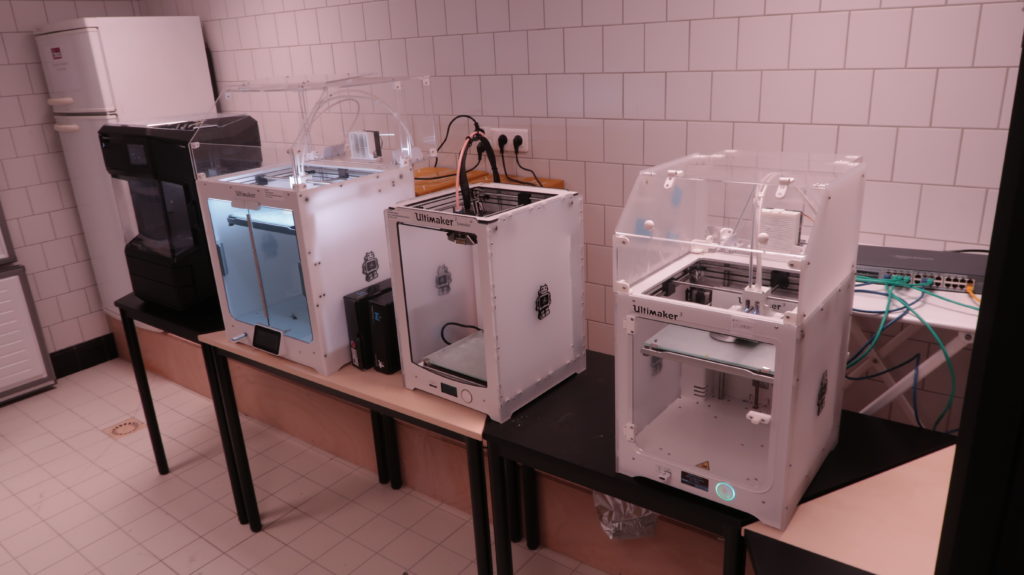
Nous avons eu besoin d’utiliser des procédés d’impression 3D spécifiques. Par exemple lors de la phase d’industrialisation, nous avons eu recours au frittage de poudre pour réaliser des pièces avec une grande précision dimensionnelle.
Nous avons aussi eu besoin de réaliser des pièces complexes à l’aide de la technologie SLA (stéréolithographie) comme la venturi (le mélangeur d’oxygène) afin d’obtenir un meilleur aspect de surface.
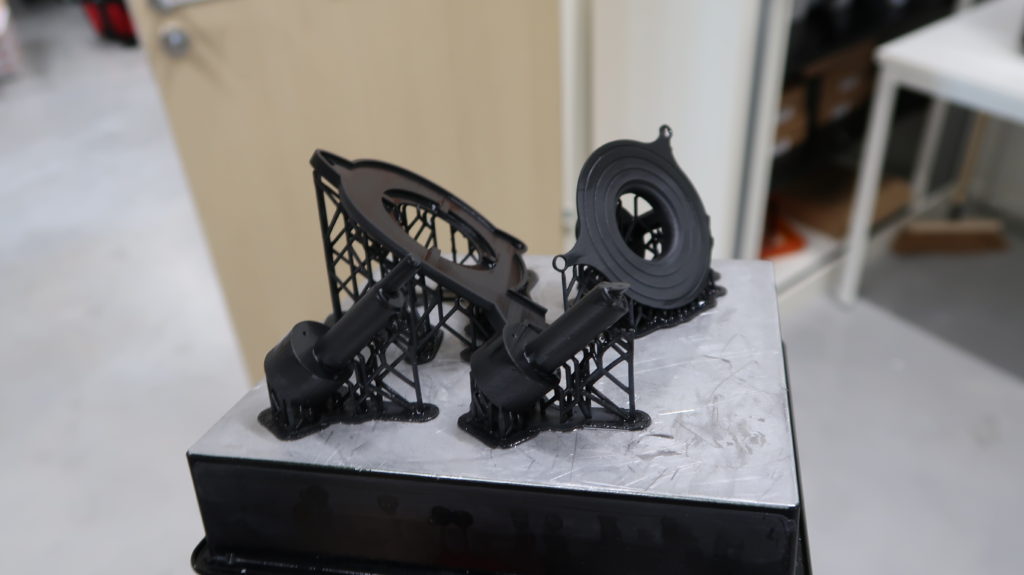
Au démarrage du projet nous ne disposions que de quelques imprimantes, puis un élan de solidarité s’est mis en place pour nous en prêter :
Des particuliers, des professionnels ou encore des écoles, ont mis à disposition leur machines et du matériel très rapidement. On a reçu toutes sortes d’imprimantes : de celles en kit personnalisées aux machines professionnelles. C’est principalement des machines FDM (dépôt de fil fondu) que nous avons utilisé car très répandu et adaptés à nos besoins de prototypes fonctionnels.
Concernant les matériaux, c’était en fonction des stocks que nous avions à disposition mais principalement du PLA car compatible avec toutes les machines et facile à imprimer. Nous avons aussi utilisé du PETG pour certaines pièces nécessitant une plus grande solidité.
Ce que je retiens de cette aventure c’est tout d’abord, cette folle aventure humaine et de superbes rencontres au sein du collectif Makers for Life.
C’était impressionnant de voir cette mobilisation collective inédite autour de ce projet solidaire, soutenu par plus de 250 bénévoles d’horizons différents.
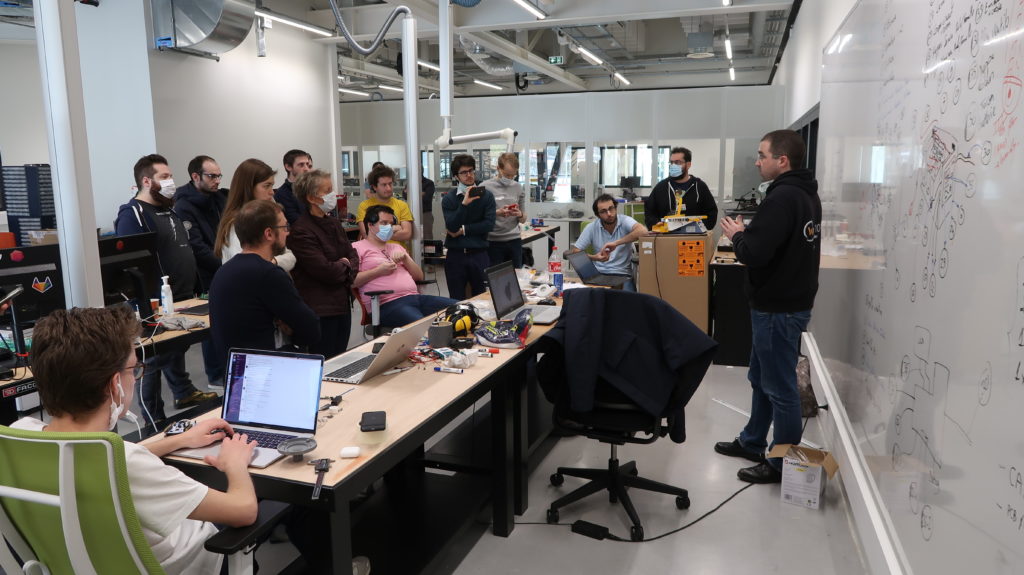
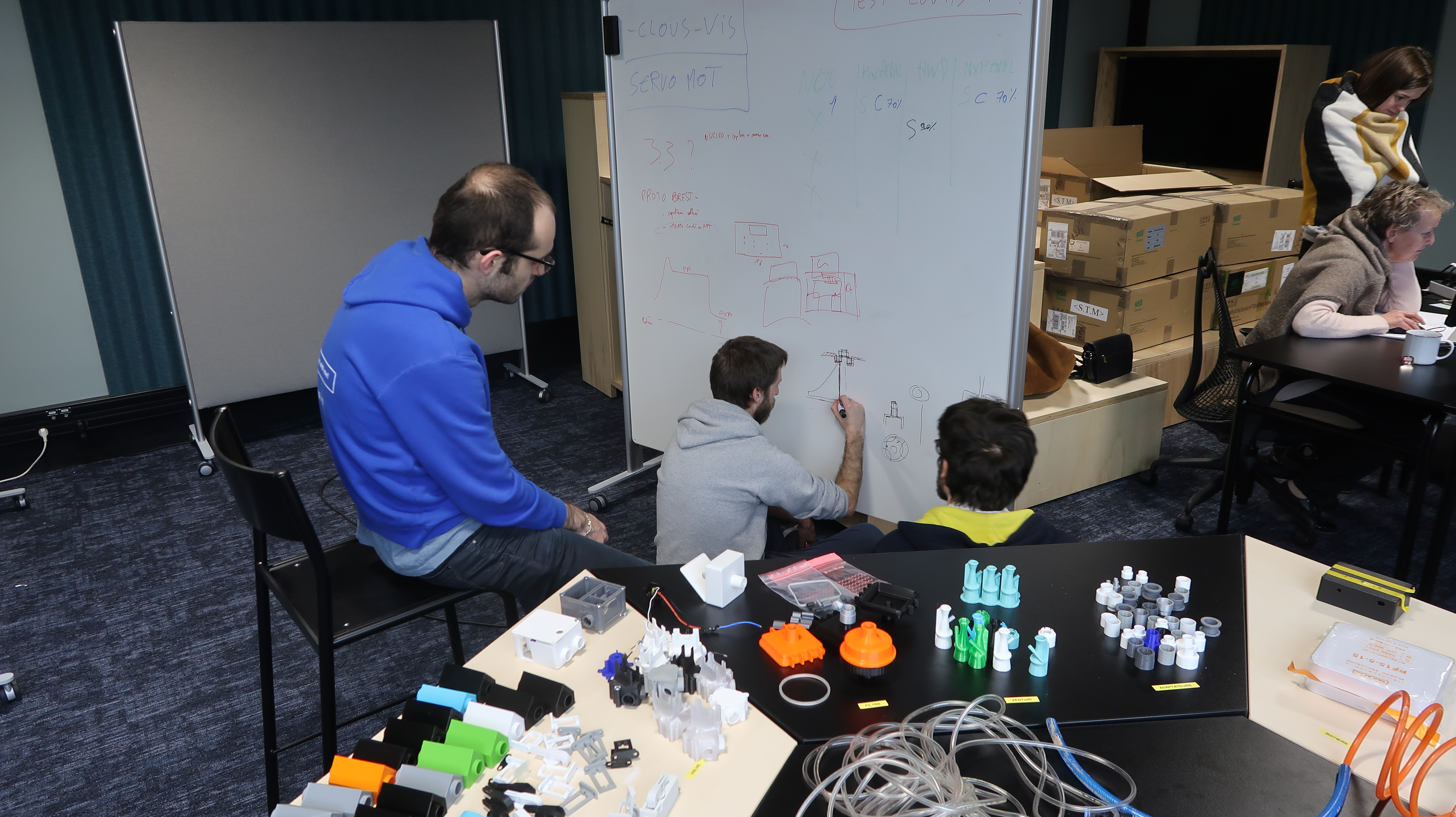
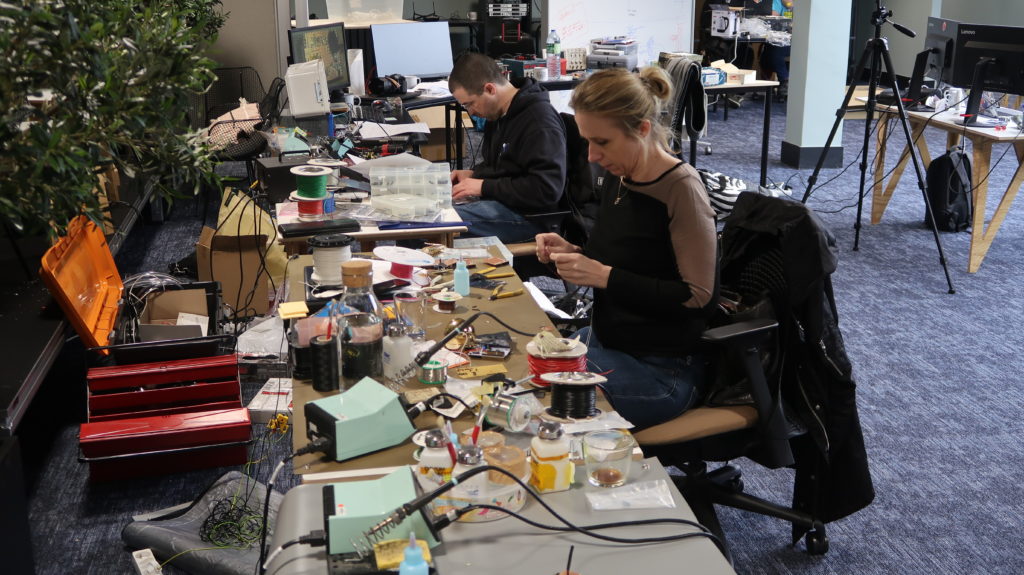
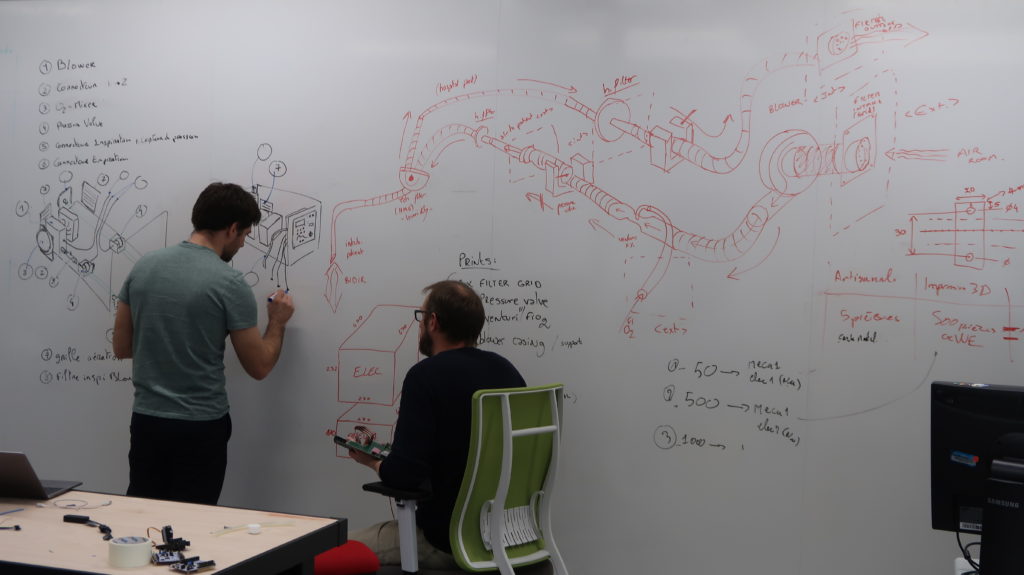
Je suis épaté par la prouesse technique du collectif et d’avoir réussi à concevoir en 3 semaines un dispositif médicale fiable malgré des contraintes fortes, telles que le confinement ou encore le manque de temps.
Et enfin je salue cette mobilisation de Makers du monde entier qui réussissent à prouver, à travers leurs différentes actions et l’intelligence collective, que la solidarité et l’entraide sont l’une des meilleures armes face aux temps de crise.